A4 |
Yes, it is possible. Three examples of synchronous measurement with multiple
units are described below.
1. When the start and stop are 1: 1
1. Input the output signal from the detector etc. as follows.
CH 1: detector # 1 start signal
CH 2: Detector # 1 Stop signal
CH 3: detector # 2 start signal
CH 4: Detector # 2 Stop signal
CH 5: detector # 3 start signal
CH 6: Detector # 3 Stop signal
CH 7: detector # 4 start signal
CH 8: Detector # 4 Stop signal
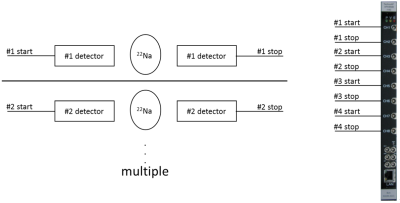
2. Start measurement in list mode and acquire / save list data.
3. Acquire time spectrum data from list data. At that time, calculate the
time difference information as follows. In addition, "TDC" below
is coarse part, "TDCFP" is fine part.
Time difference information 1:
CH 2 [TDC * 256 + TDCFP] - CH 1 [TDC * 256 + TDCFP]
Time difference information 2:
CH 4 [TDC * 256 + TDCFP] - CH 3 [TDC * 256 + TDCFP]
Time difference information 3:
CH 6 [TDC * 256 + TDCFP] - CH 5 [TDC * 256 + TDCFP]
Time difference information 4:
CH 7 [TDC * 256 + TDCFP] - CH 8 [TDC * 256 + TDCFP]
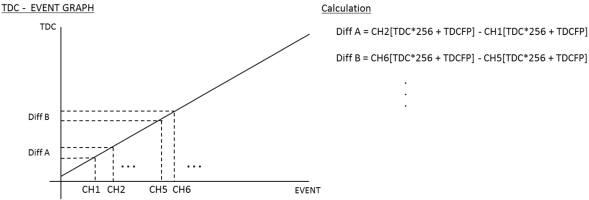
2. When the start signal and the stop signal are one to multiple
1. Enter the start signal to CH1 of each board (B0 and B1). Input the
stop signal from CH2 to CH8 of each board. Input signals of the same timing
to CH1.
NOTE: In order to decide start timing of CH1, input fast pulse with small
jitter.
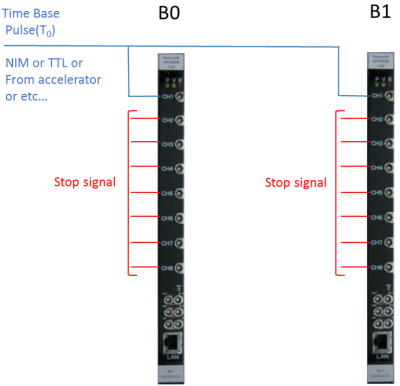
2. Start measurement in list mode and acquire / save list data.
3. Acquire time spectrum data from list data. At that time, calculate the
time difference information as follows. The following "TDC" is
the coarse bit value and "TDCFP" is the fine bit value.
Time difference information 1:
CH 2 [TDC * 256 + TDCFP] - CH 1 [TDC * 256 + TDCFP]
Time difference information 2:
CH 3 [TDC * 256 + TDCFP] - CH 1 [TDC * 256 + TDCFP]
Time difference information 3:
CH 4 [TDC * 256 + TDCFP] - CH 1 [TDC * 256 + TDCFP]
Time difference information 4:
CH 5 [TDC * 256 + TDCFP] - CH 1 [TDC * 256 + TDCFP]
Time difference information 5:
CH 6 [TDC * 256 + TDCFP] - CH 1 [TDC * 256 + TDCFP]
Time difference information 6:
CH 7 [TDC * 256 + TDCFP] - CH 1 [TDC * 256 + TDCFP]
Time difference information 7:
CH 8 [TDC * 256 + TDCFP] - CH 1 [TDC * 256 + TDCFP]
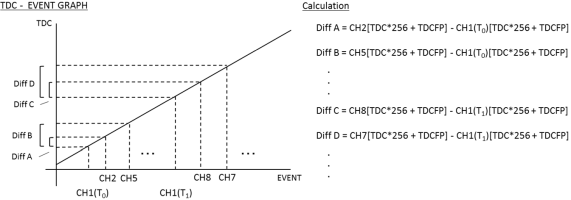
3. When the start signal and the stop signal are multiple to multiple.
Measure board 0 (hereinafter B 0) for start signal input and board 1 (B
1) for stop signal input.
1. Connect the signals you want to measure from CH2 to CH8 on each board.
Connect a common NIM signal or TTL signal to CH1 of each board.
NOTE: In order to decide start timing of CH1, input fast pulse with small
jitter.
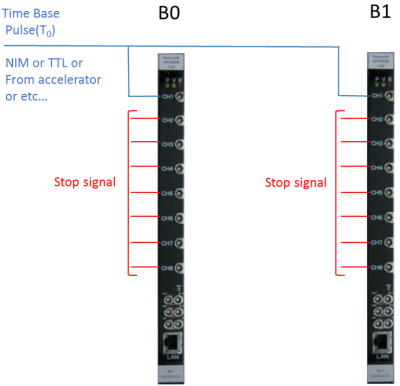
2. Start measurement in list mode.
3. Initially, input 1 pulse signal to CH1 of each board.
4. Then input the signal you want to measure from CH2 to CH8.
5. Acquire time difference information from saved list data.
First, correct the time information in the board. Subtract the TDC value
of CH1 from each TDC value of CH2 to CH8.
B0 internal correction:
data 0 '= B 0 CH 2 [TDC * 256 + TDCFP] - B 0 CH 1 [TDC * 256 + TDCFP]
data1 '= B0 CH3 [TDC * 256 + TDCFP] - B0 CH1 [TDC * 256 + TDCFP]
B1 inside correction:
data 2 '= B 1 CH 2 [TDC * 256 + TDCFP] - B 1 CH 1 [TDC * 256 + TDCFP]
data 3 '= B 1 CH 3 [TDC * 256 + TDCFP] - B 1 CH 1 [TDC * 256 + TDCFP]
Next, based on the corrected TDC value, time difference information can
be obtained by subtracting the TDC value of start board B 0 from the TDC
value of stop board B 1.
Time difference information:
Diff X 0 = data 2 '- data 0'
Diff X 1 = data 3 '- data 1'
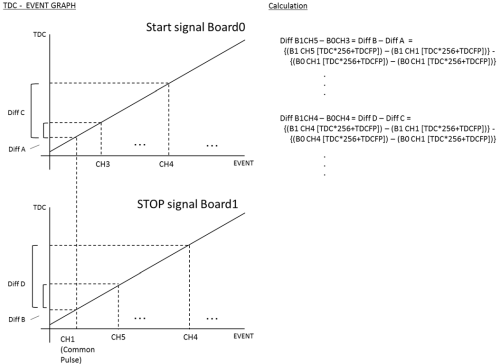 |